Productiva Bioreactors : 'One Pot' Solution for high value products
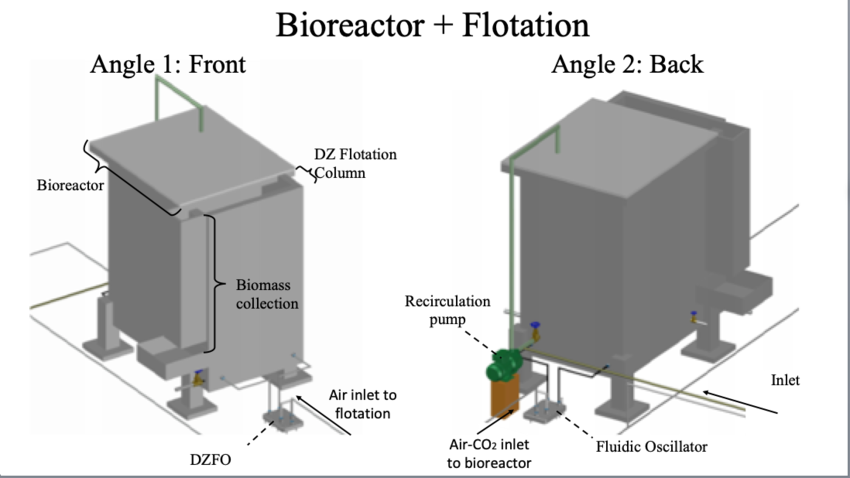
Productiva Bioreactors
'One Pot' Solution for high value products
Reepel's bioreactors have the lowest OPEX and highest yield for a given CAPEX.
Several patent families cover our 'one-pot' system which incorporates production and separation in the same reactor, Reepel Productiva bioreactors have the following major advantages:
1. we have the highest yield for lowest energy input.
2. we have the highest downstream separation efficiencies for biomass separation and product recovery (including liquids) for the lowest operating cost.
3. we have the most efficient gas delivery system on the market enabling low cost carbon dioxide and air injection whilst achieving supersaturation at ambient pressure using our 'microbubble bank'.
4. Our unique reactor simultaneously controls: nutrient availability, gas transfer, inhibitor removal and environmental conditions enabling strain specific optimisation.
5. Our low cost continuous ozone disinfection and biofilm removal achieves 5-6 log disinfection
6. Low cost continuous separation of intracellular lipids from algal cell walls has been demonstrated - even hard to extract sources such as lignocellulosic biomass
Our processes are robust and fast, achieving up to 10 fold increase in productivity whilst collapsing OPEX.
Productiva reactors are highly scalable, can be modularised, and have been demonstrated at 500kl reactor volume, while downstream downstream processes have been demonstrated at 1600kl scale.
Accelerated growth
Microbubble technology maximises both flux and rate of oxygen, carbon dioxide and other gas transfer into solution. Simultaneous to the transfer of gas to liquid, volatile metabolites and respiration gases transfer equally fast the reverse direction. And where a bubble bank is created, solids can be continuously removed by flotation.
The combination of continuous delivery of carbon dioxide into solution, removal of inhibitory metabolites and removal of solid biomass accelerates algal growth, increases yield and collapses operating cost. Our systems are highly reproducible and consume minimum energy.
The strain growth curve C.vulgaris under specific growth conditions determined by the project requirement. The takeaway message here is not the actual growth rate but rather the differential growth rate between control and Reepel Productiva bioreactors. Variations in feedstock, strain, strain stability, media used, light, gas input (flue gas or CO2 or just air), ambient temperatures, temperature of incoming gas, liquid temperature, liquid recycle rate, etc .
It is less well known that 35-60% of bioreactor operating costs are absorbed in downstream separation and processing. Downstream overheads increase significantly with higher levels of biomass separation and purification. For biomass recovery, anticipated downstream separation costs equate to around 40% of the total operating cost.
Reepel's technology provides a convenient means of continuous product separation, collapsing downstream process costs. By combining growth, separation, product recovery and inhibitory compound removal we not only accelerate growth but also collapse overall operating costs, and financial performance.
Downstream processing
There are three major aspects to downstream processing - separation and extraction :
Separation
1. Solid-Liquid separation: Dissolved air flotation (DAF) is a highly scalable and low cost process used to separate solids ( especially at lower concentrations), in a continuous manner. This process is extensively used across the drinking water and biotechnology sectors, especially for large scale, high throughput systems. Flotation is the preferred process because it eliminates the need for filtration and centrifugation. Both filtration and centrifugation carry high capital and operating costs, and for certain configurations operate intermittently to enable unloading and cartridge removal. Flotation is typically 1-3 orders of magnitude lower in capital cost compared to alternatives. One of the largest bioreactors incorporating continuous flotation for product recovery was the Pruteen fermenter built for production of single cell protein at 50,000 tonne/annum scale..
Novel laminar flow microbubble flotation was invented (in 2017) as a low cost alternative to DAF. Smaller bubbles have higher surface energy driving attachment to algal cells. Smaller “building block” bubbles increase floc stability under laminar flow conditions. Laminar flow ensures better floc stability, which delivers a high level of separation with minimal disruption. Reepel has demonstrated low cost recovery for solid based, solid and liquid based flotation systems of oil, algae/particle, or oil+particle/algae separations. An example of separation is seen in the image below.
2.Liquid-liquid separation:
Generally speaking, liquid-liquid separations are difficult and energetically intensive because liquid metabolites are typically present in a solid/liquid mixture at relatively low concentration and microorganisms maybe temperature sensitive making separation difficult. In a similar manner to distillation, relative volatility is typically used as a measure of separability. Main cost components are sensible heating which is the cost of heating the liquid up to its boiling point from ambient, which is typically 80% of total heating cost to which is added the liquids latent heat. Reepel's patented technology brings the advantage that, unlike conventional distillation, only the latent heat is required to perform the separation which makes up 20% of typical distillation operating costs. The overall cost of performing the liquid liquid separation is further reduced using other design factors, which brings about a step change reduction in operating cost while increasing separation efficiency compared to conventional, vacuum or azeotropic distillation.
Reepel's process has been deployed in several industries for ammonia separation from anaerobic digestors, ethanol removal from bioethanol fermentation and butanol and acetaldehyde from the biofuel production..
Example of what is known as Microbubble Flotation as innovated by Desai. This is different to other approaches for microflotation, significantly lower energetics than DAF, and provides advantages in terms of simultaneous removal of oil and particles (algae in this instance). Process can be sped up (using a slightly higher OPEX) or slowed down (reducing OPEX) depending on process requirements. 99.995% removal can be obtained and efficiency increases with increase in loading.
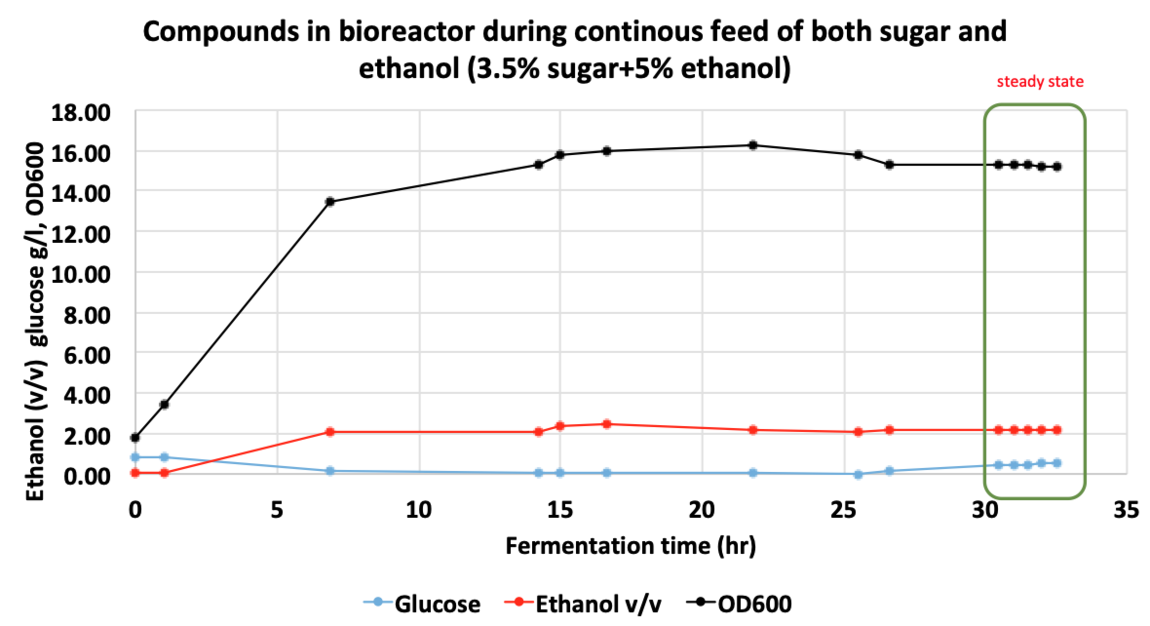
Example of ISPR obtained by microbubble technologies courtesy of Perlemax Ltd. and Prof. David Leake (University of Bath) and his team. Continuous extraction of ethanol was obtained from a bacterial bioethanol production process which resulted in null inhibition (always below the limit for inhibition) and total bioethanol production increase was subsequently obtained.
Extraction and Lysis
Reepel technology can provide a convenient means of lysing cells without addition of cell wall breaking chemicals as a means of separation and extraction of intracellular metabolites. Conventional thermal techniques incur high energy input to break cells and need separate downstream processing to separate components which can be damaged by the action of heat.
Reepel has demonstrated its lysis technology on a number of strains including lignin rich trains significantly reducing energy required and eliminating the need for chemical lysing agents.
Reepel has further demonstrated In situ disinfection and or flotation to remove undesirable contaminating species ( for example, Halomonas contamination of a D.salina culture) without reducing the algal cell viability. And have further demonstrated selective flotation for a mixed consortial culture with negligible loss in cell viability.