Advanced bioreactor technology for production and downstream separation
Low Cost CO2 Remediation and Upgrade
Reepel has designed a range of bioreactors which integrate proprietary microbubble production enhancement, in situ product separation, downstream solid separation, and disinfection technologies for a variety of purposes. One such example can be used for CO2 capture, remediation and conversion into valuable products applying a circular economy route.
Our reactors can operate mixotrophically or autotrophically via specially designed frequency-specific lights and sensors. Due to the use of the proprietary technologies above, the reactors achieve extremely high algal growth rates and total yield with significantly reduced operating costs.
Capital cost is reduced in line with the level of intensification via increased capital efficiency and reduction in downstream processing systems.
Examples where they have been used include systems which can be optimised to produce low-cost feed or fertiliser from CO2 and wastewater as feedstock in a highly consistent and reproducible manner.
With our sustainable fertiliser partner, our fertiliser solution makes remediation and conversion of waste CO2 into fertiliser, a commercially viable proposition, concomitant to reducing real emissions/ decarbonisation -directly and indirectly via substitution.
The DZ-ABRs are designed to be tuneable to meet specific growing conditions for efficient production of either biomass or metabolites which include high value chemicals - we see commercially significant improvement in performance of metabolite production as measured by production cost and quality of products produced.
CO2 from higher emissive industries
By virtue of the step change in growing efficiency, DZ-ABRs are especially suitable for remediation of CO2 to produce multiple compounds even with CO2 rich flue gas.
Whilst this is more expensive when considering flue gas from conventionally emission-intensive industries such as cement, glass, steel, coal, etc. due to the requirement of additional unit operations to remove dioxins or other dangerous products, the DZ-ABR is still a viable option compared to market competitors.
We have achieved up to 90% reduction in capital cost and >70% reduction in operating cost when compared to industrial competitors.
Image below shows versions of earlier pilot technology on a UK Steel site, with only minor mass transfer enhancements which still managed 6-fold improvement over comparator. There have been significant improvements in comparator technologies, but DZ-ABRs have superseded the work by multiple orders of magnitude in overall performance and capability.
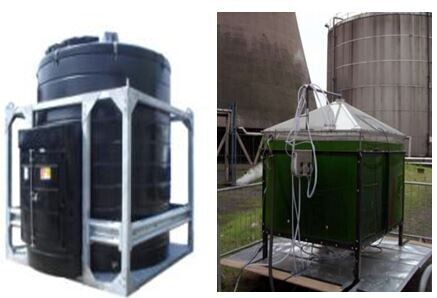
Pilot trials on the original early prototype using older technology at a major steel works in the UK. The technology was used to provide feasibility for biodiesel production with flue gas injection. Despite being an earlier technology prototype, the team obtained 6-fold improvement over conventional systems used as comparators. The trials were performed in conjunction with on-site staff. However, the comparator technologies have advanced but so to have the DZ-ABRs which have orders of magnitude better performance than the original pilot reactor, significantly lower CAPEX and OPEX, and possibility for in situ product removal, downstream solid separation (biomass), and disinfection.
Nutrient Recovery from Waste Streams
A different variant of the DZ-ABR can be used , with appropriate design , for nutrient recovery from wastewater. This ensures expensive nutrients or hard to source nutrients such as phosphorous and potassium are recovered instead of being 'destroyed' in the treatment process. This is able to produce a high P &K ratio fertiliser component, which has higher bioavailability than conventional fertilisers and result in higher yield. De Siqueira et al. (2020) ( doi: 10.1016/j.scitotenv.2020.138138 ) and Alvarez, et al (2021) (doi: 10.1016/j.algal.2021.102200.) provide excellent references for this point.
Whilst this is a standalone approach, partial CO2 sequestration and nutrient remediation can also be combined into a single process, absorbing micronutrients, heavy metals, nitrogen and phosphorus/potassium. The combined remediation system for the modified DZ-ABR carries a 10-fold reduction in capital required and >95% reduction in operating overhead, resulting in a reduction in energy consumed to be potentially <0.05kW/kg of biomass (depending on feedstock).
Depending on the nutrient composition of the feed, the resulting biomass can be used as a fertiliser additive, so long as heavy metals are compliant with local standards.
We have partnered with a leading award-winning sustainable fertiliser company to provide an integrable solution for wastewater systems from Anaerobic Digesters.
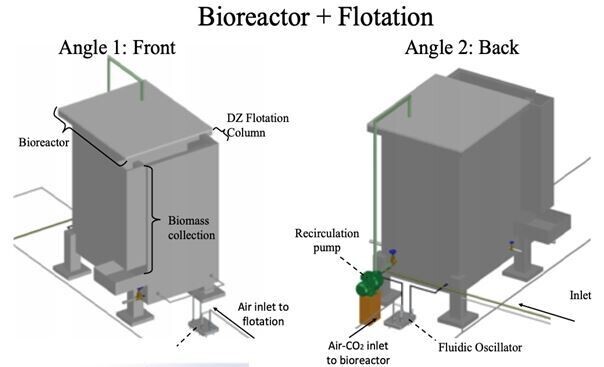
DZ-ABRs for high value product generation
Reepel's advanced bioreactors have typically the lowest OPEX and highest yield for a given CAPEX. Our patents and IP cover our integrated approach which incorporates production, metabolite separation, disinfection, and downstream separation.
DZ-ABRs have the following advantages:
1. highest yield per capita energy input
2. highest downstream separation efficiencies for biomass separation at a given OPEX
3. in-situ product removal for product removal / metabolite removal is performed at a very low OPEX due to negating the need for 'paying' for sensible heating
4. most efficient gas delivery system enabling low-cost gas injection whilst achieving supersaturation at ambient pressure using the 'microbubble bank' approach
5. reactor can have appropriate control systems in place, using IoT with specific targeted lights and control
6. low-cost advanced oxidation technologies for disinfection and biofilm removal achieves 5-7 log disinfection
7. low-cost continuous separation of intracellular lipids from algal cell walls has been demonstrated - even from hard to extract sources such as lignocellulosic biomass
Our processes are robust and fast, achieving up to 10-fold increase in productivity whilst significantly reducing OPEX. These are from tested values and can be higher due to particular strain affinities for nutrient access or inhibition rates from metabolite production.
Accelerated growth
Our mass transfer technology maximises both flux and rate of oxygen, carbon dioxide and other gas transfer into solution. Using background technology developed in R&D company, we have the ability to produce microbubbles of the smallest size theoretically possible in a given system , cf. Desai et al, 2018 - https://doi.org/10.3390/en11102680.
Smaller bubble size is excellent for mass transfer due to high surface area to volume ratio exhibited by these microbubbles.
Conventionally ,mass transfer occurs where there is a differential to the saturation pressure in a given system , and systems such as agitators, blades, membrane based systems, or fine bubble systems can achieve high levels of mass transfer and achieve 70-90% of gas saturation, albeit at extremely high operating costs.
Turbulent Microbubble generation methods are able to reach saturation (100%) relatively easily. Due to the small size of the bubbles, they are also able to achieve higher than 100% saturation due to presence of entrained bubbles with a slow-rise velocity. The bubbles are present within the solution and rising slowly due to their size, but do not dissolve immediately as the saturation level has been reached. This presents a unique situation wherein if an organism utilises some of the dissolved gases, the slow rising entrained bubbles immediately dissolve in this liquid , providing saturation , and acting as a pseudo-saturation approach.
The disadvantage in turbulently generated microbubbles is that due to the method of generation, this process expends high levels of energy while the turbulence breaks or coalesces a good proportion of the produced bubbles.
Reepel's approach is to produce microbubbles via the DZFO technology in a laminar manner. This results in significant energy reduction for production, whilst higher efficiency for microbubble bank to be created, i.e. achieving pseudo-supersaturation at ambient pressure.
The combination of continuous delivery of carbon dioxide into solution, removal of inhibitory metabolites and removal of solid biomass accelerates algal growth, increases yield and collapses operating cost. Our systems are highly reproducible and consume minimum energy.
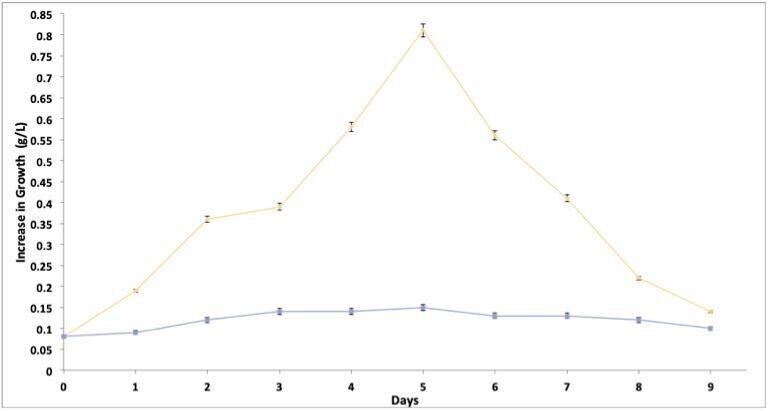
The strain growth curve C.vulgaris under specific growth conditions determined by the project requirement and operational requirements. Due to highly variable growth rates obtained due to specific feedstock/media, operating conditions, and other operational paradigms including strain batch, please use differential growth rate between control and our mass transfer enhancement system. Variations in feedstock, strain, strain stability, media used, light, gas input (flue gas or CO2 or air), ambient temperatures, temperature of incoming gas, liquid temperature, liquid recycle rate, are some controllable parameters which have a significant influence on algal production rate. A differential growth rate enables a more robust understanding of the technology ceteris paribus.
It is less well known that 35-60% of a typical bioreactor operating costs are absorbed in downstream separation, extraction, and processing. Downstream overheads increase significantly with higher levels of biomass separation and purification. For biomass recovery, anticipated downstream separation costs equate to around 40-50% of the total operating cost.
Reepel's technology provides a convenient means of continuous product separation, which significantly reduces downstream processing costs. By combining growth, separation, product recovery and inhibitory compound removal, the overall OPEX reduction and increased capital efficiencies can benefit the overall process significantly.
Downstream processing
There are two major aspects to downstream processing - separation and extraction :
Solid-Liquid Separation
Dissolved air flotation (DAF) is a highly scalable and low cost process used to separate solids ( especially at lower concentrations), in a continuous manner. This process is extensively used across the drinking water and biotechnology sectors, especially for large scale, high throughput systems. DAF is the preferred process because it eliminates the need for filtration and centrifugation. Both filtration and centrifugation carry high capital and operating costs, and for certain configurations operate intermittently to enable unloading and cartridge removal. DAF is typically 1-3 orders of magnitude lower in capital and operating cost compared to alternatives. One of the largest bioreactors incorporating continuous flotation for product recovery was the Pruteen fermenter built for production of single cell protein at 50,000 tonne/annum scale.
Novel laminar flow microbubble flotation, DZ Flotation, as a low cost alternative to DAF. Smaller bubbles have higher surface energy driving attachment to algal cells. Smaller “building block” bubbles increase floc stability under laminar flow conditions. Laminar flow ensures better floc stability, which delivers a high level of separation with minimal disruption. Reepel has demonstrated low cost recovery for solid based, solid and liquid based flotation systems of oil, algae/particle, selective flotation, or oil+particle/algae separations which is <10% of the OPEX of a conventional DAF system.
The DZ Flotation approach coupled with Desai Foam Flotation with the latest innovations is available as Featured Article for the October 2023 issue of the Johnson Matthey Technology Review:
https://doi.org/10.1595/205651323X16778518231554
Liquid-liquid separation
Generally speaking, liquid-liquid separations are difficult and energetically intensive because liquid metabolites are typically present in a solid/liquid mixture at relatively low concentration and microorganisms maybe temperature or pressure sensitive making separation difficult. In a similar manner to distillation, relative volatility is typically used as a measure of separability.
Main cost components are sensible heating which is the cost of heating the liquid up to its boiling point from ambient, which is typically 80% of total heating cost. 20% of the cost is the latent heat.
Unlike conventional distillation, only the latent heat is required to perform the separation which makes up 20% of typical operating costs, as per our in situ product removal approach. The overall cost of performing the liquid liquid separation is further reduced using other design factors, which brings about a step change reduction in operating cost while increasing separation efficiency compared to conventional, vacuum, or azeotropic distillation.
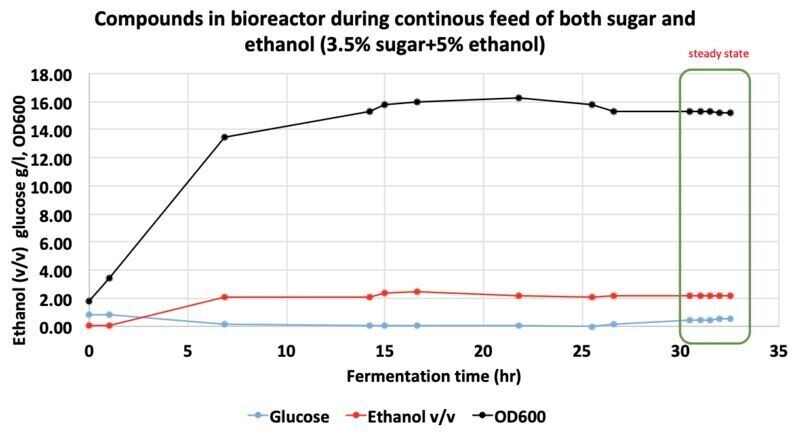
Example of ISPR using by microbubble technologies courtesy of Perlemax Ltd. and Prof. David Leake (University of Bath) and team. Continuous extraction of ethanol was obtained from a bacterial bioethanol production process which resulted in null inhibition (always below the limit for inhibition) and significant total bioethanol production increase was subsequently obtained.
Extraction and Lysis
Reepel technology can provide a convenient means of lysing cells without addition of cell wall breaking chemicals as a means of separation and extraction of intracellular metabolites. Conventional thermal techniques incur high energy input to break cells and need separate downstream processing to separate components which can be damaged by the action of heat.
Reepel has demonstrated its lysis technology on a number of strains including lignin rich trains significantly reducing energy required and eliminating the need for chemical lysing agents.
Reepel has further demonstrated In situ disinfection and or flotation to remove undesirable contaminating species ( for example, Halomonas contamination of a D.salina culture) without reducing the algal cell viability. And have further demonstrated selective flotation for a mixed consortial culture with negligible loss in cell viability.